Introduction to Hastelloy C-276
Introduction to Hastelloy C-276
Brief introduction of steel grade (steel grade) nickel-based corrosion resistant alloy C-276 (Hastelloy C-276)
Hastelloy C-276, Hastelloy® C-276, NS334, UNS N10276, national standard: 00Cr16Ni60Mo16W4
C-276 is a nickel-chromium-molybdenum alloy containing tungsten, which is known for its corrosion resistance in various corrosive media. Due to the high content of molybdenum, it is resistant to localized corrosion such as pitting. Because of the low carbon content, the precipitation of carbides during the welding process is minimized, so the resistance to intergranular corrosion of the heat-affected zone of the welded joint can be maintained.
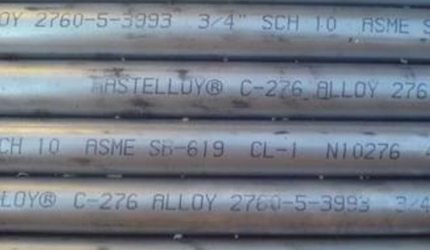
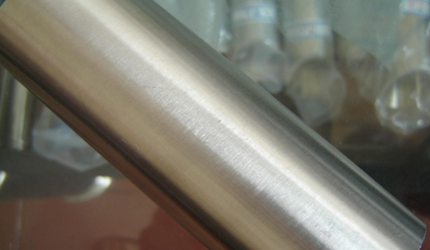
Development History
00Cr16Ni60Mo16W4 (C-276) alloy came out in 1965. After 1970, it was produced by out-of-furnace refining process (AOD, VOD) to obtain ultra-low carbon (C≤0.02%) and high purity alloy intrinsic quality. In order to reduce the sensitivity and brittleness of intergranular corrosion after welding and hot forming of 0Cr16Ni60Mo16W4 (Hastelloy C) alloy, to overcome the serious shortcomings of solid solution treatment after welding or hot forming of Hastelloy C alloy, in addition to low carbon content (C ≤0.02%), it also reduces the amount of silicon in the alloy to ≤0.08%. Reducing the amount of carbon can reduce the amount of carbide precipitation in the alloy; reducing the content of silicon can reduce the amount of precipitation of intermetallic phases in the alloy, thereby achieving the purpose of improving the alloy's intergranular corrosion resistance. At the same time, the plasticity, toughness and formability of the alloy have also been greatly improved.
Chemical composition and organizational characteristics
The typical controlled chemical composition of C-276 alloy is shown in Table 1, which is characterized by low carbon and low silicon. The structural characteristics are the same as Hastelloy C alloy, except that the number of carbides and intermetallic phases in the alloy is reduced.
C-276 features
C-276 can reduce the pressure during welding due to its extremely low carbon and silicon content. Like other nickel alloys, it is ductile, easy to form and weld, and has excellent resistance to stress corrosion cracking in chloride-containing solutions (austenitic stainless steel is prone to such degradation). With high chromium and molybdenum content, it can resist oxidizing and non-oxidizing acids, and has excellent resistance to pitting and crevice corrosion in the presence of chlorides and other halides. In addition, it has strong resistance to sulfide stress cracking and stress corrosion cracking in sour oilfield environment.
C-276 corrosion resistance
⑴ General corrosion Generally, the general corrosion resistance of C-276 is equivalent to Hastelloy C.
⑵ Localized corrosion. When sensitized or cooled after welding at 600~1150℃, there are still secondary carbides and some intermetallic phases precipitated in this alloy, which still affects the welding application of C-276 alloy under certain medium conditions. use.
In 5%FeCl3+10%NaCl solution, tested at room temperature for 72 hours, C-276 alloy has no pitting corrosion in either the welded state, the solid solution state, or the post-weld heat treatment state. In some media, C-276 alloy pitting resistance test results.
The results of the crevice corrosion test conducted in 10% FeCl3 show that C-276 is also good in crevice corrosion resistance.
⑶ Accelerated corrosion test The accelerated corrosion test is to quickly determine whether the corrosion resistance of C-276 meets the needs of the actual factory's corrosive environment. The medium selected for the accelerated corrosion test is generally more severe than the actual use conditions. For Ni-Cr-Mo type corrosion resistant alloys, hydrochloric acid bending test and iron sulfate test are required as required.
The hydrochloric acid bending test is to test in 10% boiling HCl acid for 24 hours, and then bend the sample 180°. Welding specimens are required to be bent perpendicular to the direction of the weld, and the middle of the bend should be located in the heat-affected zone. After bending the sample, observe whether there is intergranular cracking under a magnification of 10 times.
The iron sulfate test system is tested in a 50%H2SO4+42g/L Fe2(SO4)3 boiling solution for 24h. If there is intergranular corrosion, the corrosion of the sample will be accelerated. For C-276 alloy, the maximum allowable corrosion rate is 1.02mm/month or 12.24mm/a.
C-276 processing performance
Welding performance C-276 alloy has good welding performance and can be welded by general welding methods without special difficulties. And TIG, MIG and manual arc welding are the most commonly used. But when used for corrosion resistance, acetylene welding is not recommended. To prevent excessive heat input during welding, special attention should be paid to submerged arc welding.
Hot and cold processing and forming properties C-276 alloy and Hastelloy C alloy have the same cold and hot processing and forming properties.
C-276 alloy can be hot forged, hot rolled, hot pressed, hot extruded, and hot formed. But compared with austenitic stainless steel, it is more sensitive to strain and strain rate, and its thermal working temperature range is narrower. For example, the recommended initial forging temperature for hot forgings is 1232°C (2250°F), and the recommended final forging temperature is 954°C (1750°F). Moderate deformation and frequent heating can provide the best results. This alloy is harder than most austenitic stainless steels and requires more energy during cold forming.
In addition, compared with most austenitic stainless steels, C-276 alloy is easier to harden and may require several passes of cold work and intermediate annealing. Cold working usually does not affect the resistance to general corrosion, and the pitting corrosion and crevice attack caused by chloride, which can affect the resistance to stress corrosion cracking. Therefore, in order to obtain the best corrosion performance, re-annealing of cold-worked parts (when the fiber elongation reaches 7% or more) is very important.
Heat treatment In the absence of special regulations and requirements, C-276 alloy undergoes solution treatment. That is, it is heated at 1121°C and then rapidly cooled. In this state, C-276 alloy has the best comprehensive properties such as corrosion resistance and mechanics.
C-276 main application areas
C-276 alloy can produce plates (including thin plates and medium and thick plates), pipes, wires, strips, bars, forgings and castings in metallurgical plants.
C-276 is used for chemical treatment, pollution control, pulp and paper, industrial and municipal waste treatment, and sulfur-containing natural gas recovery.
C-276 has strong corrosion resistance to pitting and crevice corrosion, uniform corrosion and stress corrosion cracking of various chemical process media (especially reducing acidic media). Because of its good corrosion resistance (even in the presence of halogens) mainly for reducing media, this alloy has become the real main force dominating various applications in the chemical industry. In chemical processing, alloys are used in parts such as heat exchangers, reaction vessels, evaporators, pipes and columns.
C-276 applications for air pollution control include chimney liners, ducts, dampers, scrubbers, flue gas reheaters, fans and fan housings.